Home / All / Gas Turbine Wheel Parts /
Custom Inconel 713 718 Alloy Forging Gas Turbine Wheel Nickel Alloy Titanium Casting
Custom Inconel 713 718 Alloy Forging Gas Turbine Wheel Nickel Alloy Titanium Casting
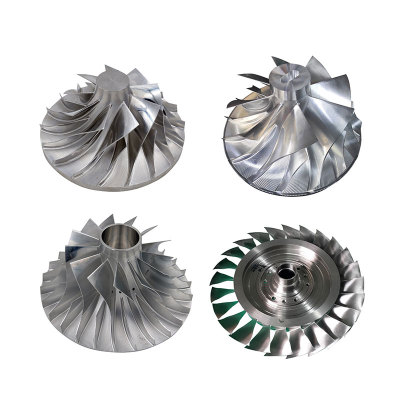
Detail Information
- Gas turbine wheels, also known as compressor or turbine wheels, are critical components within gas turbines. These wheels play a central role in the functioning of a gas turbine, which is widely used for power generation, aviation, and industrial processes. Here's an introduction to forging gas turbine wheels:
- 1. Purpose: Gas turbine wheels serve as a fundamental component of the turbine and compressor sections of a gas turbine engine. They are responsible for compressing incoming air, which is mixed with fuel and ignited to produce high-velocity exhaust gases that drive the turbine, ultimately producing power or thrust.
- 2. Material: Gas turbine wheels are typically forged from high-strength, high-temperature materials like nickel-based superalloys (e.g., Inconel) or titanium alloys. These materials can withstand the extreme temperatures and stress encountered in gas turbine operation.
- 3. Design: The design of gas turbine wheels is critical to their efficiency and performance. They have aerodynamic shapes, including blades, vanes, and shrouds, optimized for air compression and energy transfer.
- 4. Manufacturing Process: Gas turbine wheels are often forged due to the strength requirements and the need to minimize defects. Forging involves shaping a heated metal billet using compressive force. This process enhances the mechanical properties and structural integrity of the wheel.
- 5. Applications: Gas turbine wheels are widely used in various industries, including aviation (jet engines), power generation (gas turbines for electricity), and oil and gas (compressor units for pipelines).
- 6. Importance: These wheels significantly impact the efficiency and power output of a gas turbine. Their design, material selection, and manufacturing quality are crucial to the turbine's overall performance and durability.
- 7. Challenges: Gas turbine wheels operate under high temperatures and stress, which can lead to issues like creep, corrosion, and fatigue. To address these challenges, manufacturers use advanced materials and coatings and employ precision engineering.
- In summary, forging gas turbine wheels involves creating robust and aerodynamically efficient components that are essential for the functioning of gas turbines. They are critical for various applications where reliable power generation and propulsion are required.
Related Products
Please send your message to us
- Name
- Tel
- *Title
- *Content
- KEEP UP TO DATE
- Sign up for our newsletter and follow us on social media
subscription
NAVIGATION
LATEST POSTS
- Introduction to high temperature alloysNov 10,2023
- About CNC machiningNov 9,2023